Do you remember the good old days when you had to stop at a red light or got stuck in a traffic jam, and you turned your engine off to save fuel? The feeling of doing something for our planet was simply wonderful – and it still is, of course. Fortunately, minding the environment has become easier than ever. After all, car manufacturers have managed to make deactivation and activation automatic. This was a significant improvement, yet in the beginning, the first ignition was accompanied by a disappointing clatter. In a next step, the starting time was introduced. This further increased the driving comfort, yet a disturbing noise remained. Curious why that is no longer the case with modern stop&start engines, and what Gates has to do with it? Read on to find out!
Using a generator as a motor?
In 2003, Gates launched its first belt-driven stop&start system. This innovation was inspired by the idea that generators and electric motors are actually not all that different. One is mechanically driven and delivers electrical energy (the generator), while the other takes up electrical charge and converts it to mechanical motion (the electric motor). Engineers realized that, with only a small modification, the generator could actually perform both functions. So why not use the generator as a motor? Since the V-ribbed belt already connects everything, just draw on it for power transmission!
MGU instead of starter: astonishing results
In Gates’ first belt-driven stop&start engine, the motor of the generator/motor unit, now called the BSG (Belt-Driven Starter Generator), started the engine. Thanks to the better transmission ratio between the MGU and the crank disc, as compared to the conventional starter, the engine started much faster. It took less than 0.3 seconds to pull the engine up above the usual first ignition speed at about 300 rpm to almost idle speed. Moreover, the driver hardly noticed the start anymore, due to the noise reduction.
So, why not use the generator during normal operation? If you want to accelerate the car, combine both engines to get more power. Moreover, you don’t waste any more valuable energy when you brake the car. Nowadays both feats are accomplished by the ‛boost’ and ‛recuperation’ modes, which reduce pollution and fuel consumption.
Interim solution: two tensioners
The belt-driven stop&start engines cause the V-ribbed belt to be pulled from alternating sides, which had never happened before. After all, when the starter is used, you start from the crankshaft, but when the car warms up and the stop&start mode is activated, you start from the generator pulley. In other words, the taut and slack sides of the belt now varied. This made it hard for a single tensioning device to control the fluctuation of force. In 2007-2008, the idea was to simply use two tensioners, but this solution came with a few drawbacks. It not only took up previous space; it also meant that car manufacturers had to develop two different layouts for the same engine, because the version with the stop&start system required additional bolting points. And, lastly, it was known that direct physical interaction of both tensioners would reduce the required tension level in the belt, to reduce friction loss and control belt slip.
Sidewinder tensioner: the latest technology
These days, the tensioners on engines offer functional modes such as boost recoup, start, generation via the front and auxiliary engine belts. The sidewinder is installed on the Alternator/Generator. It controls the BSG via two separate belt pulleys, which do not move independently of each other. This guarantees optimum belt tension with minimum bearing loads, which means less wear in the system and thus a long service life for the components.
Some variants:
Micro-V® E-Start™ belt
Obviously, all these new technologies put the V-ribbed belt under much greater stress: belts for cars equipped with a belt-driven stop&start system are subject to significant dynamic and vibration loads. Today, the electric motor delivers up to 80 Nm on a tiny pulley, resulting in shear forces within the ribs that are up to ten times higher. Here, too, a leap in development has been made in order to offer excellent resistance and keep pace with the requirements. As the use of the usual standard belts would lead to failure, Gates has developed a special Micro-V® E-Start™ belt. This belt features an aramid-based cord that increases tensile strength. Moreover, the Micro-V® E-Start™ belt is outfitted with a special adhesive rubber that ensures the necessary belt stability.
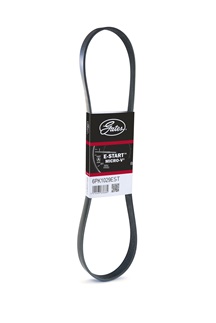
To
find the right belt for your vehicle, please consult the
Gatesautocat online catalogue or the Gates mobile app.