The automotive industry is dynamic and its technology has continuously evolved to meet stringent environmental regulations as well as to enhance driving comfort. A significant innovation in this evolution is the Start-Stop system. Introduced over two decades ago, it has since undergone substantial advancements. Belt Starter Generators (BSG) and Gates E-Start™ Micro-V® Belts play crucial roles in modern Mild Hybrid vehicles. These components contribute to fuel efficiency and ensure a smoother, quieter driving experience, making them indispensable for sustainable automotive solutions.

- An Inside Story of Start-Stop and BSG Technology
The first Start-Stop systems began to appear in the early 2000s. They have helped to reduce emissions by saving fuel when the engine is not required, such as when the vehicle is at a red light.
In vehicles with Start-Stop, some models start the engine through the alternator instead of the starter motor. In such cases, the alternator temporarily becomes an electric motor, also known as a Belt Starter Generator (BSG). When the BSG is converted to an electric motor, it pulls the accessory belt engaged to the crankshaft, thereby turning the crankshaft and restarting the engine after it has been stopped.
Such systems require higher belt tension and grip to operate smoothly, but have the great advantage of being faster than a conventional starter. They are much quieter, too.
To match these operational requirements, Gates developed a more robust belt capable of transmitting the necessary traction and enduring many starts over its lifetime.
This Start-Stop system belt (see image.3) has improvements such as Aramid cord for added strength and durability (1) and improved EPDM rubber material for quieter operation (2). The rubberized fabric on the back side of the belt adds extra protection, plasticity, and resistance to temperature variations (3).
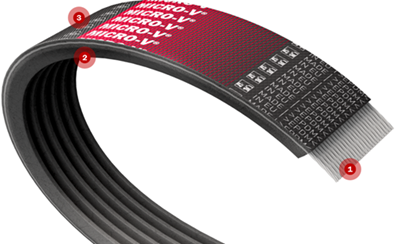
Image3
- Evolution of the Start-Stop Technology System
This system evolved significantly with the introduction of a two-tensioner system (see image.4) to suit diesel-engine vehicles of the time, thereby improving the grip of the belt on the alternator pulley.
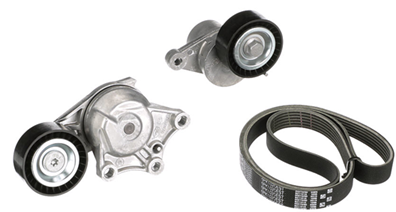
Image 4
This (image.5) shows how the engine traditionally pulls the belt. The tensioner located between the alternator pulley and the crankshaft works harder in this case because it is the point where the belt has less tension (1).
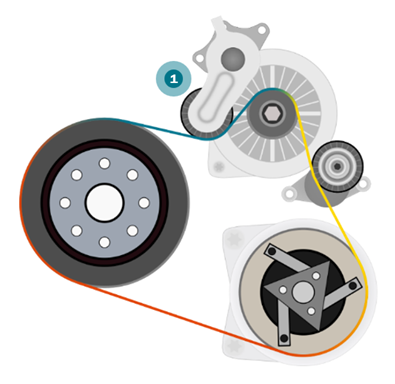
Image 5
- Combustion engine Start-Stop mode
This (image.6) shows how the forces in the system are temporarily modified. During start-up, the alternator becomes the starter motor and pulls the belt while the engine is stopped. This tensions the point between the alternator pulley and the crankshaft, pushing the tensioner housed there (1). Meanwhile, the other tensioner tightens the belt before the alternator pulley on the slack side (2) to avoid losing traction at start-up.
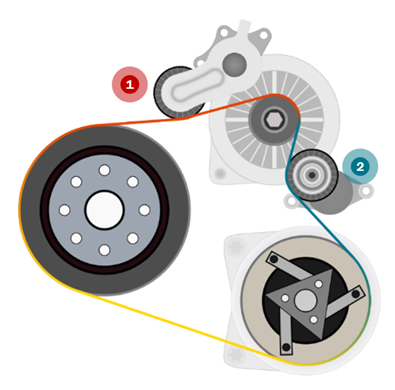
Image 6
Mild Hybrid systems can be seen as an evolution from Stop-Start systems with a BSG. The improvement found in these systems is determined by the BSG’s capacity to assist the combustion engine at certain times, such as when starting after a traffic light or when extra torque is required (Boost Mode). Thanks to this new system, large numbers of vehicles in the EMEA parc have reduced their emissions of polluting gases and are able to meet more stringent anti-pollution standards.
To implement the extra torque offered by the BSG and fully utilize regenerative braking, tensioners have had to evolve along with the system. In a system with two independent tensioners, the performance of regenerative braking and boost mode would be limited. However, using a sidewinder tensioner makes it possible to transfer all the power with less tension.
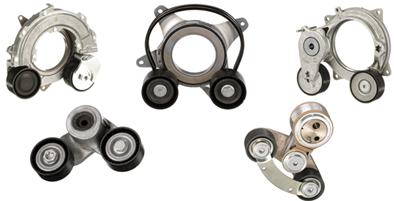
Image.7 shows a range of different sidewinder designs, all of which work in a similar fashion.
This novel tensioning system (image 8) operates on a mechanical connection between the pulleys on both sides of the alternator pulley. When one part of the belt is tensioned, the part with less tension is instantly tensioned by the rotary motion of the tensioner. Let’s see how it works in different modes of operation.
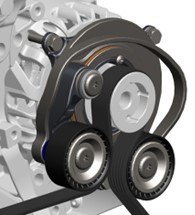
Image 8
This mode (image.9) operates similarly to traditional Start-Stop systems. At ignition, the BSG, which becomes an electric motor, pulls the belt to rotate the crankshaft and start the engine. Thanks to the mechanical connection, when the alternator applies torque to the belt, the belt pushes the tensioner pulley on the tensioned side. The tensioner then rotates on itself (1), applying tension on the slack side of the belt (2), preventing it from slipping on the alternator pulley. This process happens very quickly and quietly, so the driver sometimes does not even notice it.
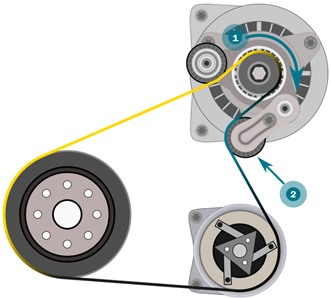
Image 9
In certain driving moments (see image.10), the BSG assists the combustion engine, such as when starting from a traffic light at low revs where the combustion engine is less efficient and the BSG brings out its maximum potential. In this mode, the same process occurs as in the start, but the BSG applies much higher torque (1) for a longer time. The mechanical connection of the sidewinder tensioner pulleys is especially important due to the high torque transmitted.
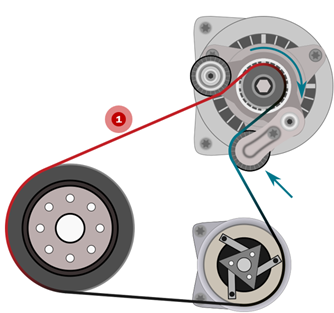
Image 10
- Regenerative breaking mode
During deceleration, the BSG takes advantage of the vehicle’s inertia to charge the battery. Consequently, the BSG shaft shows more opposition to being rotated (see image.11), increasing the belt tension (1) and forcing the tensioner to position itself as shown in the illustration below.
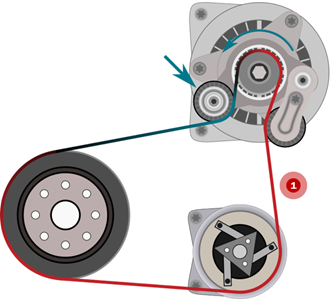
Image 11
Depending on the vehicle and equipment, coasting mode may be possible in some situations. This mode allows the combustion engine to be switched off while traveling at a certain speed (between 55 - 160 kph) to take advantage of inertia and consume less fuel.
Through these modes of operation, the sidewinder tensioner constantly rotates on itself, adapting the tension to the alternator's side or the other according to its current operating mode. As these tensioning devices are more stressed and work continuously, they often have a maintenance period set by the vehicle manufacturer. The period typically ranges from approximately 90,000 - 140,000 km. Gates offers replacement kits, where both the tensioner and the belt are supplied, to ensure a greater guarantee of repair.